Autoclaved Aerated Concrete
Concrete having a cellular structure is called aerated concrete. It is an artificial stone, in which the entire volume is penetrated by pores. The hardening under pressure with steam in an autoclave served as its name. The pressure in the autoclave is above atmospheric and is about 12 atmospheres, the temperature of processing products is 190 degrees.
Autoclaved concrete is obtained from cement, sand, quicklime, water with the addition of a little aluminum powder. During the chemical reaction of lime and aluminum powder during foaming of the mixture, pores with a diameter of up to 3 mm filled with air are formed.
A construction made of such material was called "Stone Tree" for combining the properties of wood and stone.
Autoclaved Aerated Concrete Properties
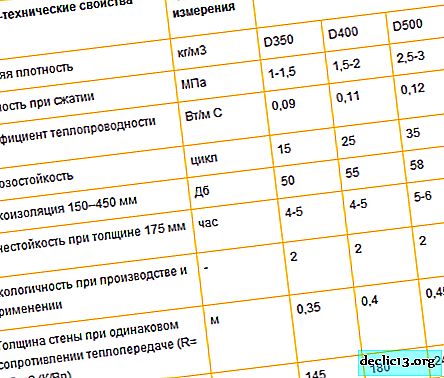
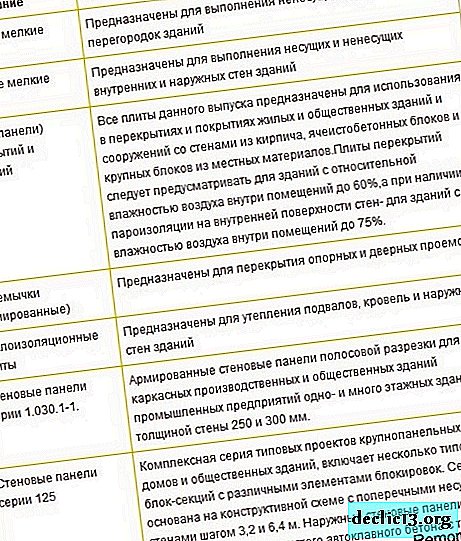

- light machining;
- eco-friendly;
- combination of stone strength and wood weight;
- high thermal insulation (coefficient of thermal conductivity - 0.12 W / m ° C);
- fireproof;
- high degree of sound absorption;
- resistant to adverse environmental conditions;
- water and vapor tight;
- durable. Compliance with manufacturing and construction technology allows you to operate buildings up to 100 years;
- does not rot.
The technology of manufacturing autoclaved aerated concrete
- Preparation of the mixture. All constituent materials in predetermined proportions are automatically mixed in automatic mode to obtain a composition having a consistency of not thick sour cream.
- Pouring into forms, getting the right block size. With periodic shock loads, half the volume of the mold is filled with the prepared mixture. Periodic vibration improves the porosity of the material. The interaction of aluminum and lime causes the release of free hydrogen, raising the mixture, which fills the volume of the form completely. The temperature reaches 80 degrees, which leads to the setting of cement. As a result, cells are formed in the shape of a sphere, filled with air with pores up to three millimeters in diameter. For high-quality production of autoclaved concrete, it is necessary to strictly comply with the manufacturing process.
- Mass hardening. Approximately 60-120 minutes are necessary for the preliminary hardening of the array, in which it will be strong enough and cut well.
- Cutting an array into finished blocks. A well-hardened mass, but remaining soft enough after the dismantling of the prefabricated form, is cut with thin strings into blocks, grooves and ridges are formed with a special tool, and pockets are made for easy operation.
- Steaming blocks in an autoclave. Finished products are placed in an autoclave. Thermo-humid treatment takes place in it for about 12 hours. Temperature - 190 degrees, vapor pressure - 12 atmospheres. Under these conditions, the material acquires sufficient strength. A special installation allows you to get blocks of autoclaved concrete of the right size.
- Packaging. Finished products are stacked on pallets and transferred to a finished product warehouse or delivered to a construction site.